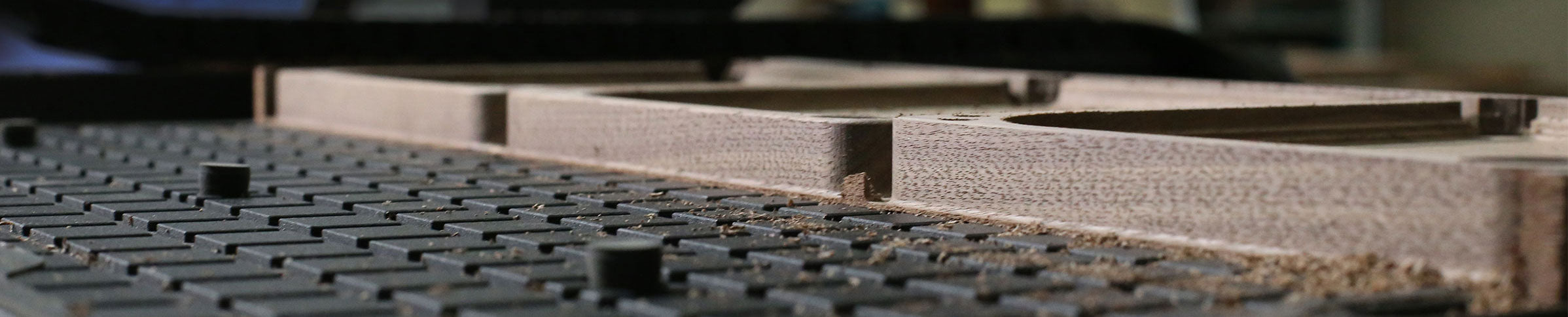
Product Instructions
Setting up and using your AirWeights Vacuum Table System is quick and easy. Please reference the step by step instructions and useful videos below. Feel free to contact us directly with any questions or issues.
What's Included:
24x24 AirWeights Vacuum Table
- 24x24 Vacuum Table Assembly
- ¾” Locating Pins (2x) - AW Install
- ½” Locating Pins (2x) - Fixture Plates, MDF+Tile Gasket
- 5/16” OD x ⅛ NPT Push-to-Connect Fitting
- Mounting Screws (14ea, 2 extra)
- Rubber Plugs (12ea, 2 extra)
- 25’ Grid Gasket (no adhesive)
- 8’ Vacuum Line (5/16” OD Polyurethane)
24x48 AirWeights Vacuum Table
- 24x48 Vacuum Table Assembly
- ¾” Locating Pins (2x) - AW Install
- ½” Locating Pins (2x) - Fixture Plates, MDF+Tile Gasket
- 5/16” OD x ⅛ NPT Push-to-Connect Fitting
- Mounting Screws (20ea, 2 extra)
- Rubber Plugs (22ea, 2 extra)
- 50’ Grid Gasket (no adhesive)
- 8’ Vacuum Line (5/16” OD Polyurethane)
5 CFM Vacuum Pump
- 5 CFM Vacuum Pump
- Mounting Feet
- Inlet Filter
- Vacuum Gauge
- Exhaust Muffler
- Male/Male Fitting
- Male/Female/Female T Fitting
- Male to 5/16 OD Push-to-Connect Fitting
9 CFM Vacuum Pump
- 9 CFM Vacuum Pump
- Mounting Feet
- Inlet Filter
- Vacuum Gauge
- Exhaust Muffler
- Male/Male Fitting
- Male/Female/Female T Fitting
- Male ½/Female ¼ Reducer (for Vacuum gauge)
- Male to 5/16 OD Push-to-Connect Fitting
Set Up and Installation
Vacuum Pump Setup
Vacuum Pump Setup:
1. Install Rubber Feet- These feet dampen the vibration. Install hand-tight only.
2. Install Exhaust Muffler onto exhaust port- Thread into place, hand-tight only.
3. Install Intake Components onto intake port:
- Apply PTFE tape on all male threads. Apply liberally so that threads can be clocked to desired position in each connection.
- Install Intake Filter to pump intake using male-male threaded adapter. Note the direction of the arrow on the filter inlet; this should point towards the pump. Filter canister may be removed for easier installation.
- Install T-adapter (male/female/female)
- Install Vacuum Gauge. Be sure to end rotation at a viewable position.
- Install push-to-connect fitting onto end of T-adapter.
4. Install a push-to-connect fitting onto one of the threaded ports on the side of your AirWeights table. There are ports on all sides for easy access depending on your specific setup.
5. Install the air line between the pump and the AirWeights table. Both sides utilize push-to-connect. Simply push the end of the air line firmly into the fitting to seal. To release the fitting, push the plastic collar towards the metal flange while pulling the air line out.
AirWeights Vacuum Table Installation
The AirWeights vacuum table is designed to attach to any CNC machine. Installation and removal of the vacuum table are both quick and repeatable, using the included locating-pin setup.
Determine Installation Location, and Install locating pins:
- Provide a clean, flat, co-planar surface to mount the AirWeights on.
- This referencing location should be saved. Once the locating holes are in place you can re-install the Vacuum Table onto the same exact spot every time, for accurate repeat machining.
- Use your machine to drill the 4 locating-pin holes into your spoil-board. Holes should be 0.25" in diameter, and 0.375" - 0.5" deep. The locations are marked with cross hairs in the table DXF File (below)
DOWNLOAD 24x24 DXF File (click here to begin download)
DOWNLOAD 24x48 DXF File (click here to begin download)
DOWNLOAD 24x36 DXF File (click here to begin download)
DOWNLOAD 16x16 DXF File (click here to begin download)
Install AirWeights Vacuum Table onto Spoil-board
- Place locating pins into "bottom left" and "top right" locating pin holes. You may face your spoilboard before installing pins to ensure flatness.
- Place the AW vacuum table onto the pins, constraining the vacuum table in the XY plane, and ensuring repeatability for every subsequent installation.
- Use the included mounting screws to secure the AirWeights directly to the spoil-board:
- Install 1 screw in each of the holes and slots along the edge of the vacuum table. (12 screws for the 24x24 table, 18 screws for the 24x48 table).
- Use a torque wrench or clutched driver to ensure equal mounting force from each screw and a uniform surface.
- *TIP: Consider using ¼-20 (or M6) threaded inserts in your machine table for easy removal and installation. This also helps control equal torque values. Mounting points are sized to receive ¼-20 Socket Head Cap Screws.
- Connect a vacuum line to the push-to-connect fittings on pump inlet, and vacuum table side-port.
- Plug all 10/20 vacuum ports using provided rubber plugs. Don’t forget to plug the touch plate corner location(s).
- Turn on vacuum pump for 10 seconds.
- Turn off pump and watch gauge. Drop should be slow, losing less than 5”Hg every 10 seconds.
QCW Vacuum Slats for Onefinity Machines- Installation
QCW Vacuum Slats - Installation Instructions
Step 1: Installing the Pump Exhaust Mufflers
- Locate the four included exhaust mufflers.
- Install them on the underside of the pump before operating.
Step 2: Setting Up the Pump Intake
- Refer to the appropriate product image on the website for the correct intake setup.
- Use the included PTFE tape generously to: - Adjust the gauge to a convenient viewing position. - Clock the intake filter with the canister pointing downward, as shown in the reference image.
Step 3: Mounting the Manifold
- Choose a convenient location to mount the manifold where you can easily access the valves.
- Securely mount the manifold in place, ensuring it is positioned for efficient air line routing.
- Important: Do not screw the manifold into the bottom of a slat, or you will breach a necessary seal.
- Confirm that the installation location allows for easy adjustments and operation of the individual slat valves.
Step 4: Selecting and Installing Air Line Fittings
- Locate the hardware box for each slat, which contains two fitting options: - (1) 5/16” OD x ⅛ NPT straight fitting - (1) 5/16” OD x ⅛ NPT 90-degree elbow fitting (recommended for cleaner air line routing)
- Choose the fitting that best suits your setup.
- Each slat has two edge inlet options for connecting air lines: - The front edge has two 1/4-inch diameter holes. - The rear edge has two 1/4-inch wide slots.
- Remove the installed ⅛ NPT plug with a 5mm hex key and install the selected fitting.
- Do not overtighten the fitting and take caution to avoid cross-threading.
- Shorter air lines yield better vacuum performance due to reduced head loss.
Step 5: Connecting the Air Lines
- Use the included 5/16" OD air line to connect each slat to the provided manifold.
- The manifold includes valves that allow you to turn each slat "on" or "off", isolating vacuum to specific slats as needed.
- Connect 1/2" OD tubing between the manifold and the pump.
- Shorter tubing is optimal for vacuum performance.
- Experiment with the full 8-foot length before trimming based on your pump placement and manifold mounting.
- Note: Our vacuum pumps should be left on the ground in a convenient location to prevent vibration from affecting your CNC frame.
Optional: Squaring Your Slats to X/Y Axes
This step is optional and can be completed at any time for precise alignment between the 1/4" holes in the top grid and your CNC X/Y axes.
Steps to Square Your Slats:
- Determine the exact locations for your slat installation. Refer to the DXF files below for default layouts and adjust as needed for accessory clearance.
- Roughly position your slats on your QCW frame. If already mounted, loosen the screws by 1/4 to 1/2 turn.
- Install the included 1/4" x 1.5" long dowel pin into your spindle.
- Jog the spindle to a suitable X/Y coordinate for one of the front-most dowel pin holes.
- Lower the spindle into a dowel hole (do not exceed 1/4" depth).
- Tighten the front-most screw underneath the dowel hole.
- Retract the spindle and jog in the Y-direction to the rear-most dowel pin hole.
- Slowly lower the spindle, ensuring the slat is squared.
- Tighten the rear-most screw underneath the second dowel pin hole.
- Verify alignment and make final adjustments.
- Fully tighten all screws (do not overtighten).
- Repeat this process for each slat.
DXF Files: For precise X/Y coordinate selection, refer to the DXF file containing your slat system geometry.
DOWNLOAD Woodworker QCW Slat DXF File (click here to begin download)
DOWNLOAD Journeyman QCW DXF File (click here to begin download)
DOWNLOAD Foreman QCW DXF File (click here to begin download)
DOWNLOAD 9"x42" Slat DXF File (click here to begin download)
Install AirWeights Vacuum Table onto Spoil-board
Your vacuum workholding system is now installed and ready for use!
If you have any questions, please refer to the support documentation or contact customer service.
Gasket Options
Holding Your Workpiece
The AirWeights Vacuum table is a versatile workholding solution, able to apply powerful and reliable vacuum clamping using several different gasketing methods. Depending on the specific needs of the job/material/shape, we offer 3 main gasketing solutions, each with specific use-cases.
Direct Mount
Direct Mount using Grid Gasket is a fast and economical way to set up a part. Simply align a gasket based on our 1” grid layout. You can achieve any shape or size, and create multiple independent vacuum zones for multiple parts.
When you are done, simply remove the gasket, and you have a clean grid pattern to create a whole new arrangement for your next cut.
With this method, you do not want to cut below the bottom surface of your part, since the table is sitting directly below the workpiece.
Follow these steps to ensure success when using the direct mount method:
- Use grid gasket (no adhesive) to create a sealed zone underneath your stock. The zone must contain at least 1 vacuum port.
- Plug all remaining vacuum ports. Don’t forget the corner(s)!
- Place your stock material over the sealed zone, making sure your stock completely covers the gasket material.
- Turn on your pump and apply downward pressure to your stock to help create a seal.
- The sound of your vacuum pump will change, pressure difference will increase and your part will be rigidly held.
- Make sure to leave a .050” “onion skin” at the bottom of your cuts when using this method. DO NOT CUT THROUGH or you may damage your vacuum table and lose vacuum pressure, depending on the gasket approach.
- Use a secondary process (trim router, drum sander, sanding whip, etc…) to remove the remaining onion skin from your part.
Material Tips: Your stock material must be flat for the vacuum table to create a seal and firmly hold your stock. If you are struggling to create a strong hold, consider using individual pieces instead of longer boards or large sheets containing multiple pieces. Always place your material concave side down and apply pressure to support vacuum sealing when seating your stock.
MDF + Tile Gasket
Tile Gasket is a quick, user friendly, and extremely versatile workholding method. The large “tile” of perforated gasket material turns the entire surface of your AirWeights Vacuum Table into one large suction surface - delivering uniform vacuum clamping across the whole table. This is amazing for organic shapes, designs with uneven outlines, or items that would be otherwise very challenging to create a gasket for.
Simply place your workpiece anywhere onto the tile gasket surface, and it will be held firmly in that spot.
Since the tile gasket is a soft foam, you can cut below your part, for fully finished through-cuts with no tabs or onion skin.
Through-cuts should be just slightly (0.005”) below your part, barely kissing the foam gasket. This minimizes damage to the gasket itself, allowing you to use one gasket many times over.
How To Apply Tile Gasket Sheet to 1/4" MDF:
NOTE: The type of MDF used is critical to this approach. We recommend using ¼” thick MEDEX from Roseburg Forest Products. Other MDF materials can work, but the material density needs to be at least 45 lbs/ft³ [720 kg/m³] to function properly with your AirWeights system. This can be counterintuitive when compared to traditional vacuum table systems found on large industrial CNCs, which move large volumes of air. Our pumps prioritize pressure difference and power efficiency. If low density materials are used, the pump will not generate a high pressure differential due to excessive flow through the MDF. Higher density MDF helps to reduce this flow, allowing the buildup of a pressure difference to create strong workholding.
- Place your ¼” MDF on the vacuum table and turn on the pump. Our pre-applied MDF+Tile Gasket assemblies have precision locating holes to accurately and repeatedly locate on the AirWeight. You can expect a reading of about -15” Hg while the MDF is leaking air through its thickness.
- Face off the minimum amount possible from the top of the MDF. Ideally .010” (0.25 mm) or less. This is primarily to achieve coplanarity between the top surface of the MDF and your machine. If you are happy with the variation in Z across the MDF surface without facing it, you can skip this step.
WARNING: Ensure the 1/2" steel locating pins are fully seated in the AirWeight and sub-flush of your facing depth. You may also face the sheet without the locating pins installed to avoid a potential crash. - Somehow mark the orientation of the MDF after facing, if you decided to. This ensures that any Z error you accounted for is maintained each time the MDF is placed back onto the AirWeight.
- Remove the MDF from the AirWeight and place it on a flat surface. Without removing the backer, place the tile gasket onto your MDF in the position you’d like to install it. Make sure your tile gasket covers the top surface of the MDF completely. *TIP: Place a heavy object on the tile gasket to maintain its position.
- Fold 1 edge over to show the backer. Peel back ~3”-5” along the entire edge, then fold and crease the backer to keep it away from the adhesive.
- Fold the gasket back over and place the exposed adhesive lightly against the MDF in the appropriate location. Adjust as necessary. Once the correct location is achieved. Apply pressure to activate the adhesive.
- Fold the gasket sheet back the other way. Slowly peel the backer off the tile gasket, allowing the sheet to naturally lay onto the MDF. Once the sheet has been rolled on, apply pressure all around the gasket to seat the adhesive.
- Place your MDF + tile gasket assembly back onto your AirWeight, making sure to maintain the same orientation as before.
- Place material on top of the tile gasket. Turn on your vacuum pump and apply downward pressure to your stock. Allow 10 to 20 seconds for pressure to build. Push and pull laterally on your material to test how secure the hold is. If you are not comfortable with the holding force, do not perform any cuts.
Tile gasket tips and tricks:
- Minimize the amount you cut through to maintain the service life of your tile gasket. Cutting deep into the gasket, or worse, cutting through into the MDF, will cause issues and leaks for the next project. You may even choose to leave a very very thin onion skin (i.e. .005”), which will simply flake off upon removal of the part. This will maintain the service life of your tile gasket. This approach requires understanding your stock thickness very very well, especially in the location where you are setting your Z0 position.
- This approach is very sensitive to flatness. If your stock material is bowed or warped, this approach may not function well.
- This approach is sensitive to surface roughness. For example, plywood with a very coarse grain will be challenging to hold. Smooth surfaces such as prefinished plywood or plastic sheets are ideal.
- This approach is sensitive to porosity. If your stock material is porous, consider a different approach or completely seal the bottom surface of your material (using sanding sealer, lacquer, blue tape, vinyl, etc...).
- Seal the edges and a 1 inch border on the bottom side of your MDF. Lacquer wood, glue, epoxy, etc... have all been proven methods. This helps to prevent leaks through unwanted areas and isolates vacuum to the tile gasket ports where it's needed.
- If you’re stock material is smaller than the surface of your tile gasket, cover any exposed tile gasket with a non-porous scrap material, such as thin sheet plastic, marker board or scraps of prefinished plywood. This helps prevent leaks in unused areas and increases holding force on your stock.
Fixture Plates
- Fixture Plates are a non-porous, semi-sacrificial surface that sits between your AirWeights vacuum table and your stock. It is meant to be cut into, allowing you to cut completely through your stock and leaving you with finished parts at the end of your program. This method provides the same level of holding force as direct mounting, but with the added benefit of cutting completely through.
- Gasket material is used on the top surface of the Fixture Plate to create sealed vacuum zones that sit within the boundary of your finished part(s). These zones must also account for any internal areas that are cut completely through, such as an internal hole. The basic rule is that there must be a seal anywhere that is completely cut through.
- There are 3 primary approaches to creating vacuum zones on a fixture plate.
Adhesive backed gasket can be recessed in a channel (commonly called in-board gasket), which should be 1/4" wide and .065" to .085" [1.65 to 2.16 mm] deep for the adhesive gasket sold by AirWeights. With the in-board approach, air channels must also be cut into the fixture plate within the gasket boundary to allow air to disperse underneath the material being held.
Adhesive backed gasket can also be used directly on top of the fixture plate (commonly called on-board gasket). Simply use the CNC to trace the outline of your part at a shallow depth, then install the gasket on the interior of that profile and drill a hole in the center. This method is demonstrated in the video below and is great for quick projects and thick stock. In some cases, the stock will float on top of the gasket, allowing complete cut-through capability without cutting into the fixture plate.
Finally, a continuous sheet of gasket material (commonly called cover gasket) can be applied to the entire top surface of the fixture plate. To create the required vacuum zones, an engraving bit is used to cut away the unwanted gasket material and create vacuum zones under each part position. This approach is great for very small and intricate parts that are otherwise very challenging to hold or require secondary processes.
All 3 of these options are valid solutions for fixture plates. - Within the sealed regions, there must also be hole for a vacuum inlet. Place a .400” [10.2 mm] diameter hole so it aligns with a channel in the AirWeights grid underneath, while still being close to centered within the gasket boundary. Smaller holes may be required for very small parts and are acceptable in those cases. Machine the holes last when making your fixture plate and DO NOT CUT THROUGH or pressure will release, your fixture plate may come loose and you may damage your AirWeight by cutting into it. Use a drill, countersink or razor blade from the backside to break through the thin onion skin left at each vacuum inlet location.
Using Your AirWeights
Start Vacuum Clamping
After setting up the appropriate gasket for your specific workpiece, you are ready to clamp your workpiece in place.
To clamp your material, place it over your gasket location, turn the vacuum pump on, and push firmly onto the top of the material, it can take a second or two for vacuum clamping force to build.
Confirm vacuum holding force by referring to the pump gauge, which should read between -18 to -25 Hg when holding vacuum. You should also confirm the vacuum hold by giving the workpiece a nice firm push and pull, physically confirming that it's being held rigidly.
With the material vacuum clamped into place, you can proceed to set your X/Y/Z Zero positions, and/or locate the corner of your workpiece. Take careful note of the Z height relative to the depth of cut in your program. Cutting too deep can risk cutting into your vacuum table. You can cut below the part if you are using tile gasket or a fixture plate.